THEY WORK SO WE CAN PLAY
Southwest Composite Works – Albuquerque, NM
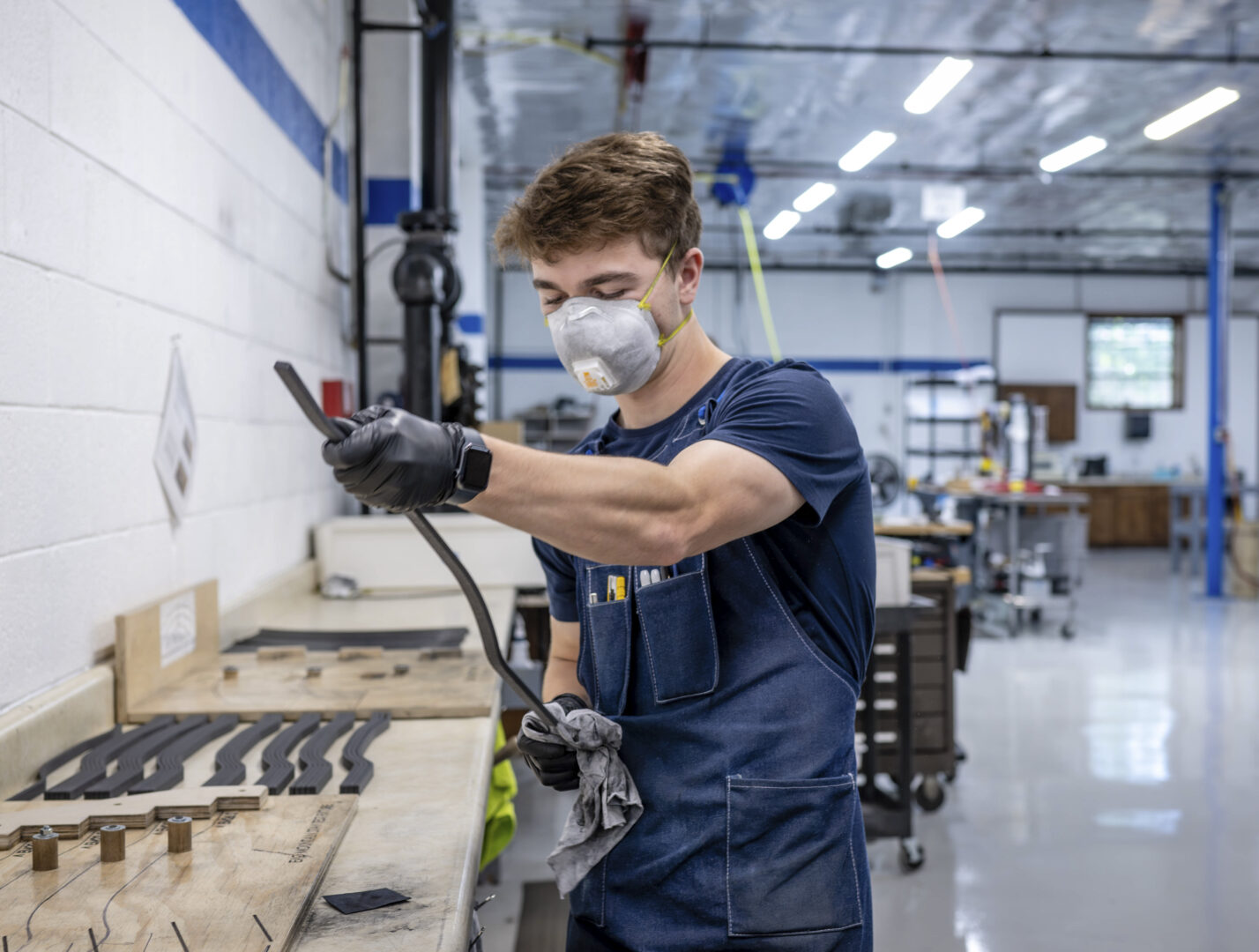
Weaned on carving wooden shapes and patterns for engines, John Groth styles himself as an old-fashioned mold maker. But now Groth and his company, Southwest Composite Works, Inc., based in Albuquerque, is at the cutting edge of the outdoor recreation industry.
His custom-made, carbon fiber pieces, which are side struts and back panels, can be found on any number of upscale backpacks, particularly those used by backcountry hunters who field strip and pack out their prey.
“Ultralight backpackers, backcountry hunters, or anyone seeking lighter solutions often find that opting for a backpack frame stay system instead of a full backpack frame is ideal,” states the company website. “The primary advantage is their lighter weight compared to a full frame.”
While the carbon fiber industry has revolutionized bicycle construction, Groth says it is a market difficult for Americans to gain ground, but the company has successfully looked to make headway in other areas instead.
For example, the bicycle industry has exploded in the use of carbon fiber in top brands in the US, but it has deep manufacturing roots in Asia. Groth explains that the bike industry shifted production to Asia about 30 years ago, and Asian manufacturers have become quite proficient at carbon fiber engineering and construction.
“There is no shortage of capable manufacturers for that kind of product. It is just the reality of a global economy. My current jobs now focus on the hunting and fishing markets, particularly big-game hunting. It is all about getting out there and enjoying the outdoors, and we want to make it easier for people to do that. Parts made from carbon fiber make for a great choice as it allows us to make things lighter and stronger,” Groth says.
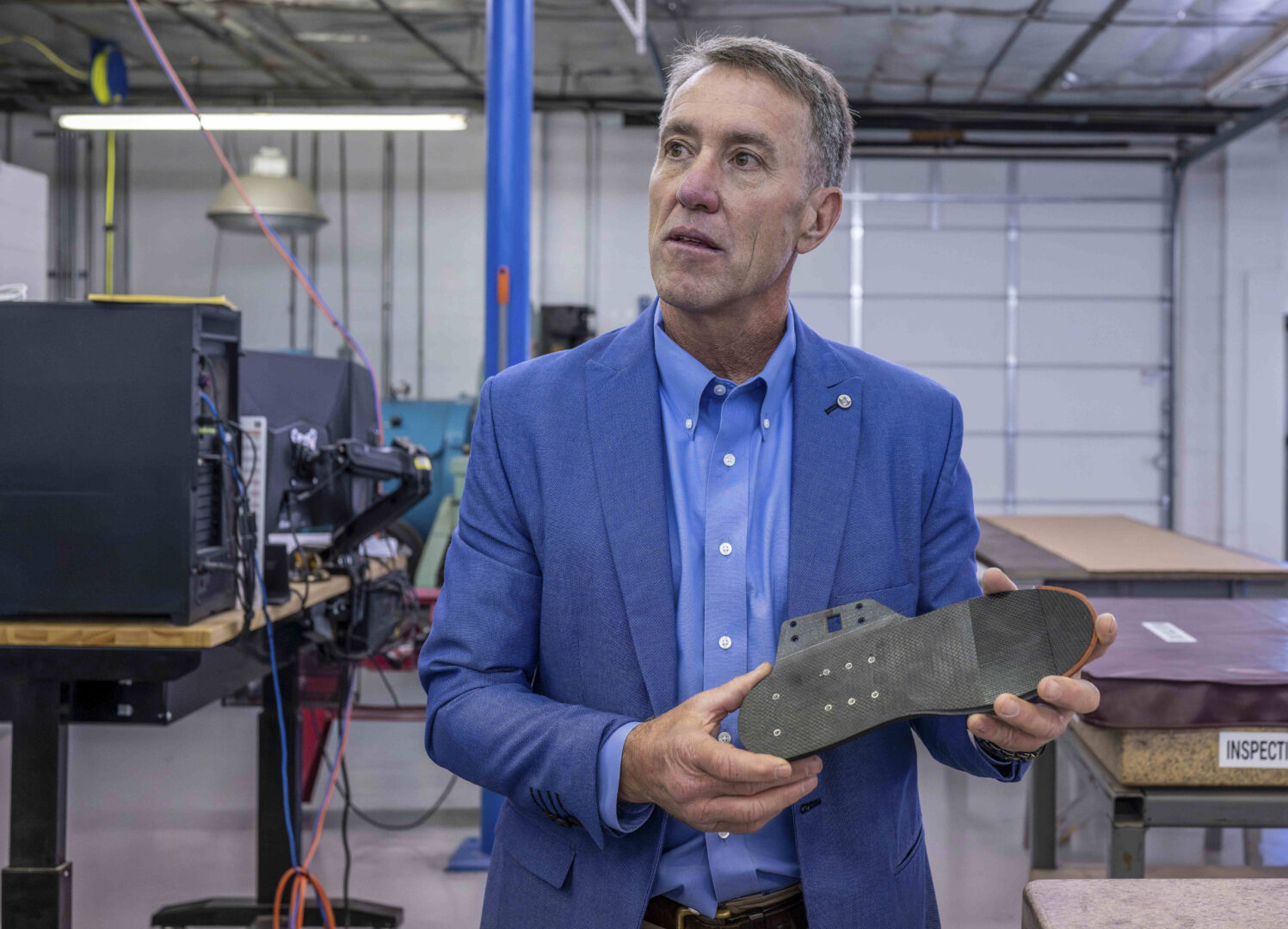
Set in a sparkling, wide-open, 15,000-square-foot shop that used to be a jewelry manufacturer, machines hummed and workers busily assembled or cut or polished, all with strict quality control.
“The greatest aspect of carbon fiber is its incredible versatility; much like wood, its strength lies in the grain. This allows us to manipulate the material in any direction we desire,” explains Groth. “Our aim is to craft a product with the desired level of stiffness, rigidity, torsional stiffness, and weight required by our clients. By utilizing multiple layers, we have the flexibility to fine-tune the material’s characteristics to achieve the exact strength our clients require.”
He takes a finished, cut strut piece and bends it, and upon letting it go, it pops right back into shape, a great example of why backpacks with carbon fiber struts are able to carry more weight than traditional struts while remaining lighter and stronger than traditional materials.
“It’s seven times stronger than steel by weight and about half the weight of aluminum in the same shape,” Groth clarifies. “Compared to a piece made of aluminum, carbon fiber parts would easily weigh half as much for the same strength. However, with aluminum, once it’s bent, it won’t return to its original shape. With carbon fiber, it can bend repeatedly until it eventually exceeds the engineering constraints.”
Creating the perfect mixture of strength and flexibility took some effort, but it was all part of the process. And that’s what makes the carbon fiber products so strong.
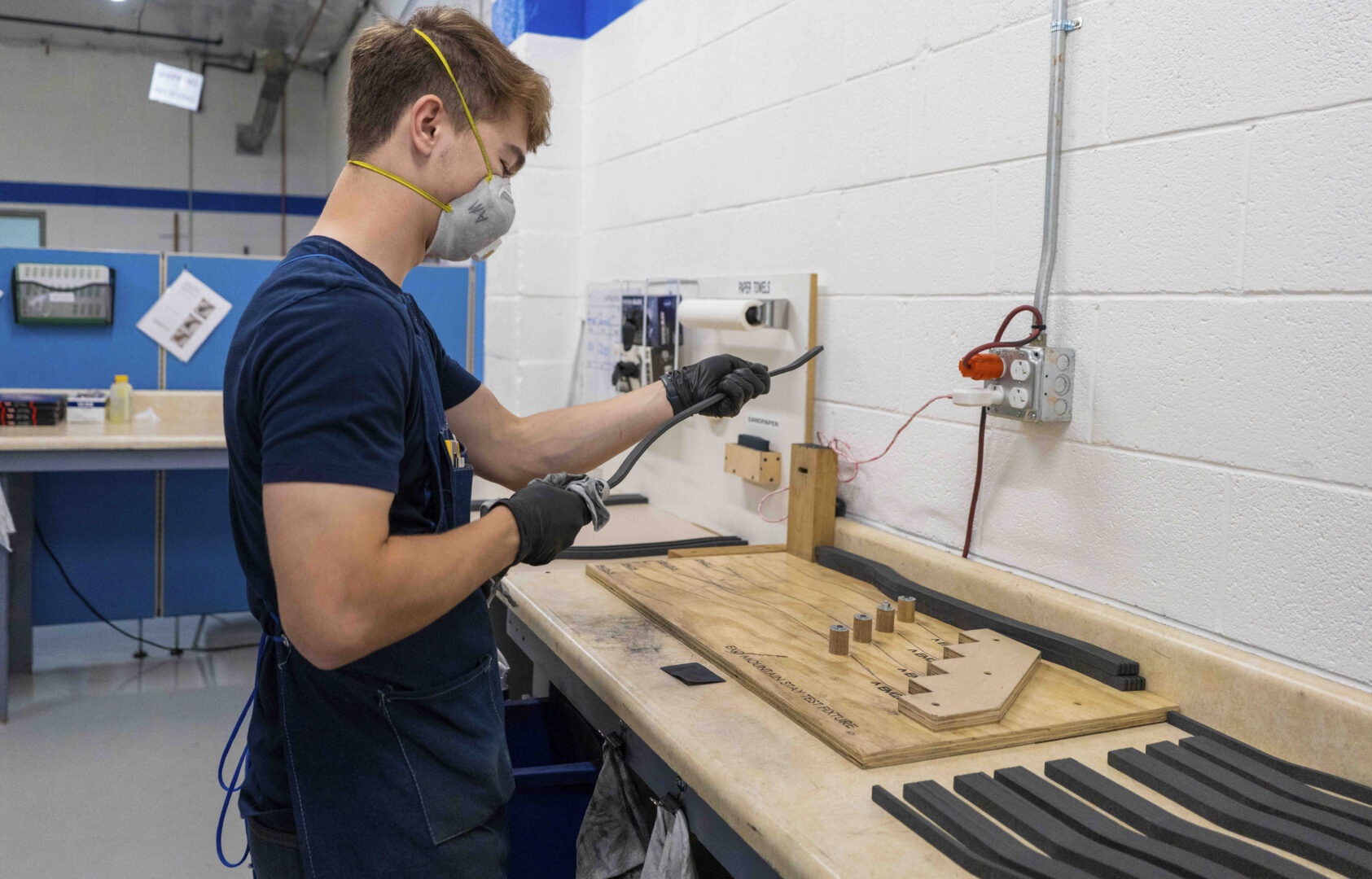
“Our approach is always to use industry best practices. One of the methods we often use with our clients is a compression molded process, using carbon fiber that is already infused with resin (super strong epoxy),” Groth says. “The pre-preg sheets of carbon are then placed on a CNC (computer-numerical-control) cutting table, where a blade cuts the carbon sheet to fit the design coded into the computer, ensuring precision and minimal fabric waste.”
Groth then added, “Using these cut pieces of fabric, we place them in a specific orientation within the mold (dictated by the characteristics and specifications we are looking for in part). Laying up the carbon this way allows us to optimize weight and strength. From there, the carbon fiber that has been placed in the mold is loaded into a heated press, where the carbon fiber and epoxy are permanently bonded together using high pressure and heat. This cures the epoxy and forms the carbon fiber into one solid piece that is ready for finishing.”
The consumers in these markets understand quality products and the higher performance carbon fiber and American manufacturing bring to products. So, they are more willing to spend the extra money for a product that is lighter and stronger and makes their activity more enjoyable, Groth says.
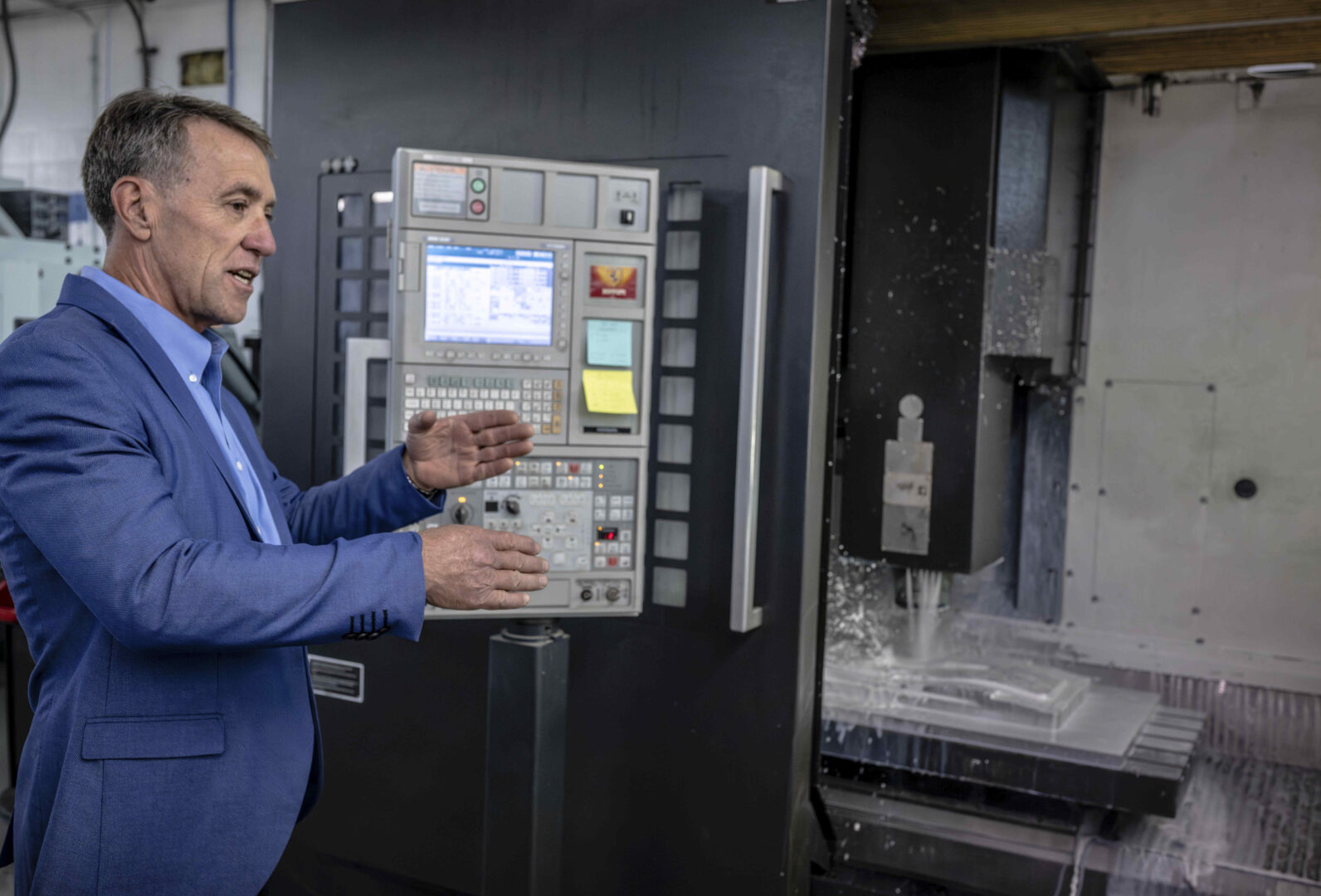
A NEW MEXICO STORY BEGAN IN THE MIDWEST
Like many folks who call New Mexico home, the state immediately appealed to Groth and his wife. In 1994, they moved from Wisconsin to Albuquerque. “We love it. We liked the weather. We liked the culture. We like everything about New Mexico,” Groth says.
As active outdoor enthusiasts, frequently backpacking, skiing, rock climbing, hunting, and fishing, the couple not only values the environment this magical state offers, but also are users of the carbon fiber products made at SWC.
Starting the company in Albuquerque was an evolution from working with a small local machinist shop doing foundry work to eventually branching off to start from scratch, gravitating towards mold making as that is what Groth knows and Albuquerque needed.
The company grew, employees, shop size, applications, and impact.
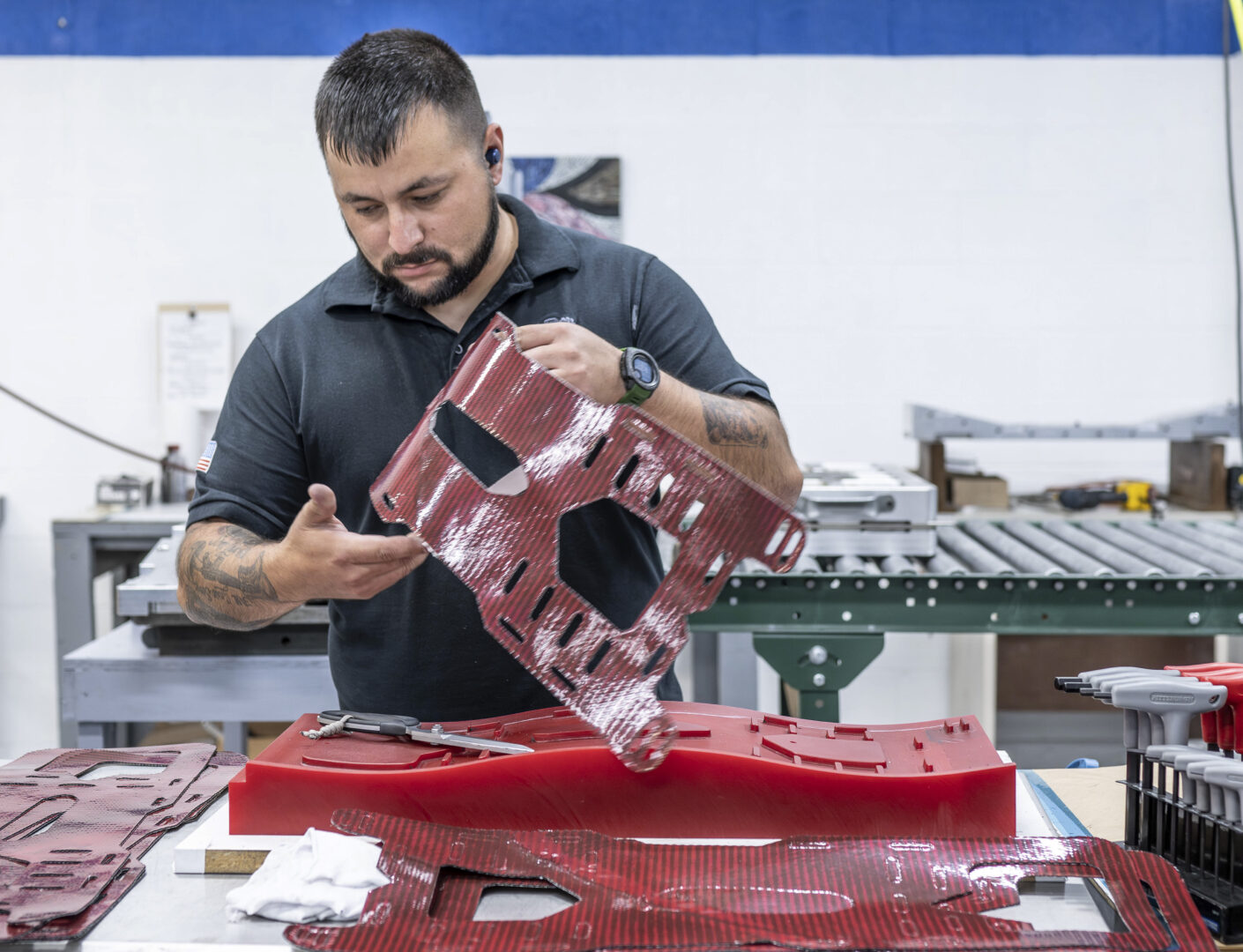
OTHER APPLICATIONS
Southwest Composite’s works can be found in other areas of outdoor recreation, as well. The company is now making ultralightweight but extremely tough and durable motorcycle handlebars for specialty Harley-Davidson motorcycles—which could not be much cooler for a Milwaukee man like Groth.
Inside the tool, a latex bladder expands as the carbon fiber wrapped around it undergoes a heat cycle, reaching 350 degrees Fahrenheit, while a high-pressure press makes sure everything stays compact. This allows the carbon fiber to match the design shape cut into the mold. This innovative method is used in the new Harley manufacturing process.
“There really is no limit to where carbon fiber can be used. Just look at the extra durable and lightweight fiberglass kayak paddles on the market now,“ Groth says. “This is also becoming a growing niche market for his business, noting that the ultimate applications for carbon fiber materials are limited only by one’s imagination.”
“This is the only job I’ve ever had,” Groth adds with a smile. “I’ve been molding and tool making since high school. I’m a journeyman. I value the craftsmanship this industry demands. As we say here at the company, we’re a shape company. We like shapes, we do shapes.”
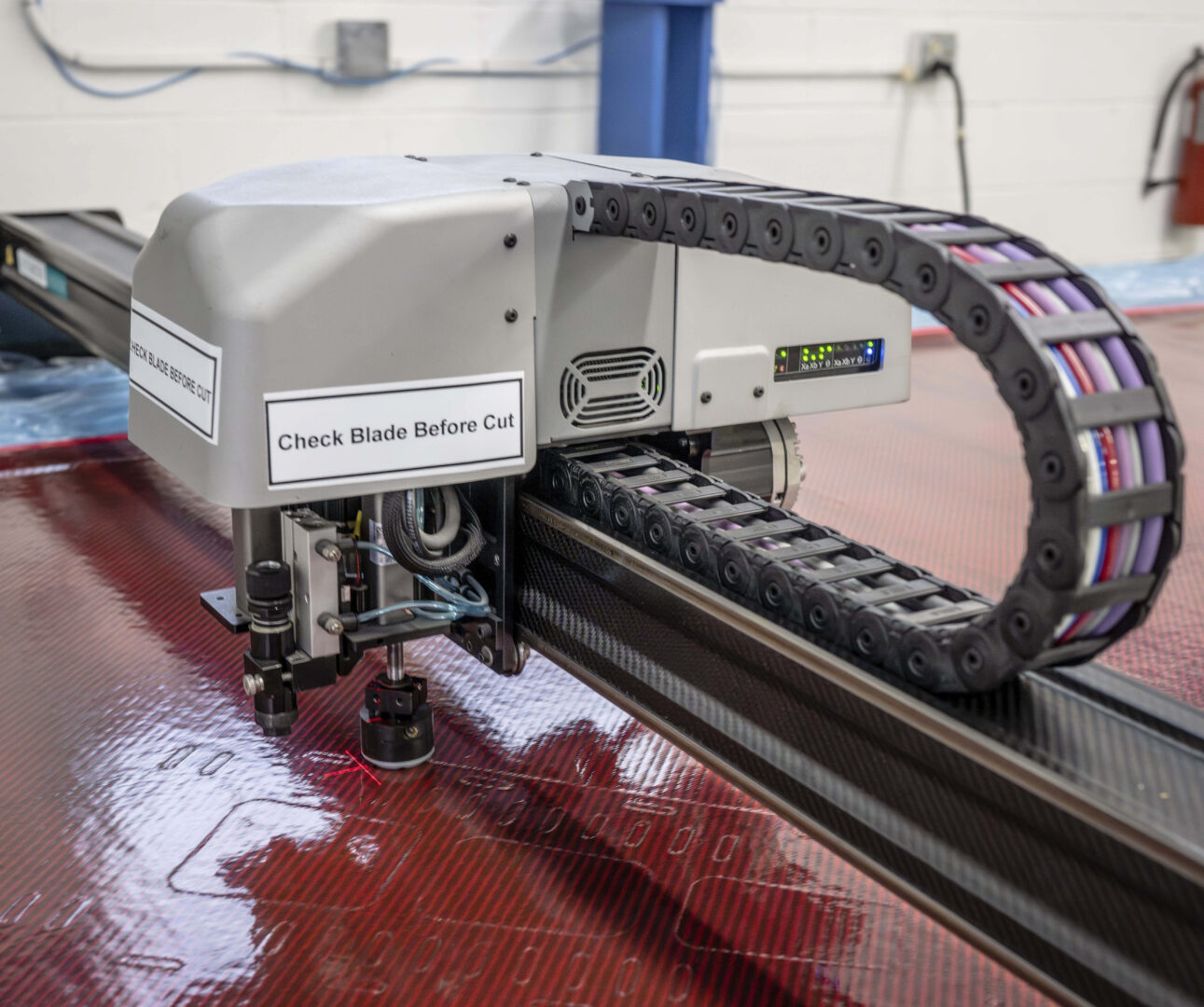
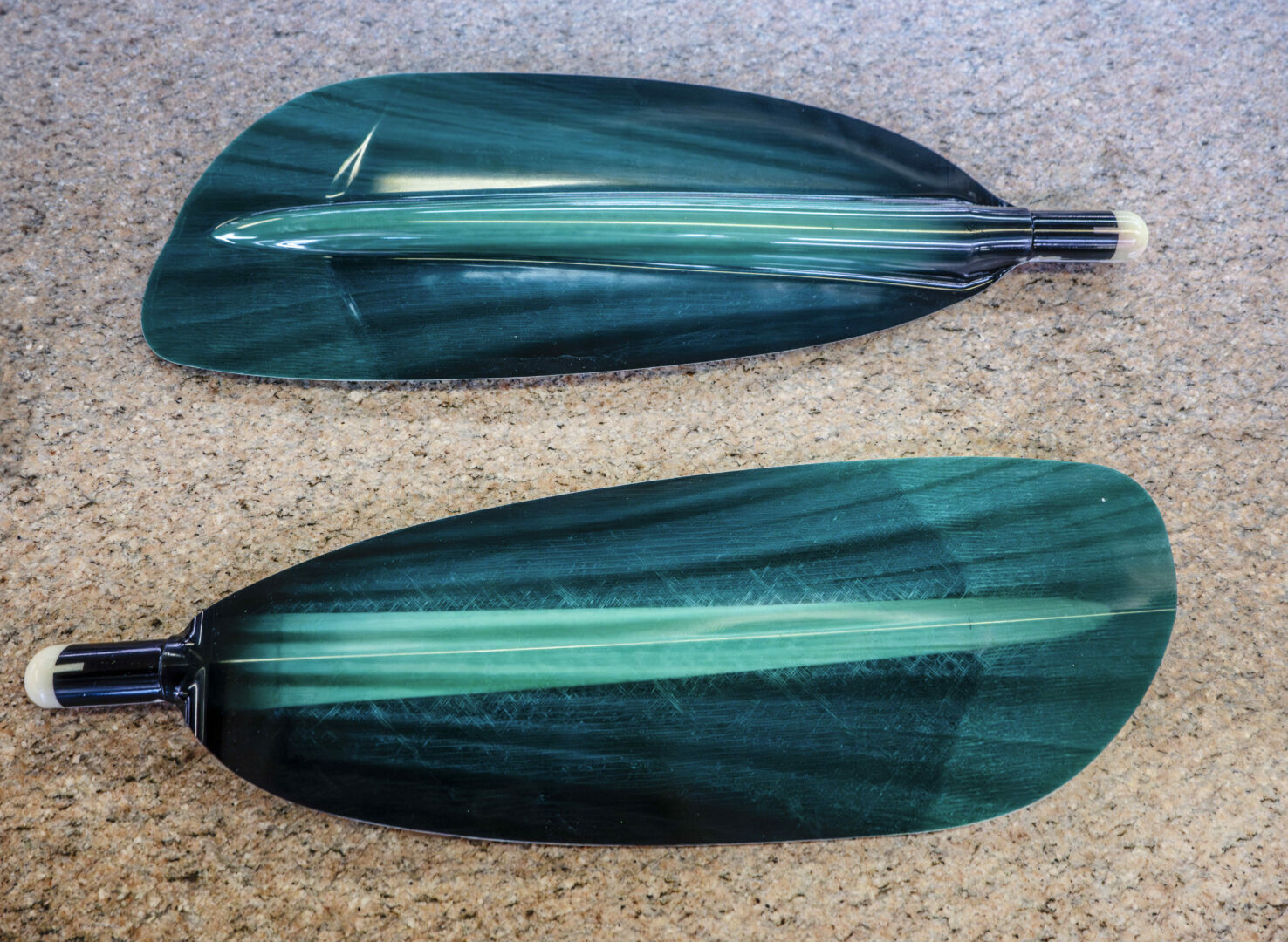
Photos by Roberto E. Rosales Photography Editorial by Glen Rosales
Southwest Composite Works – Albuquerque, NM